Precision Injection Molding: Transforming the Manufacturing Landscape
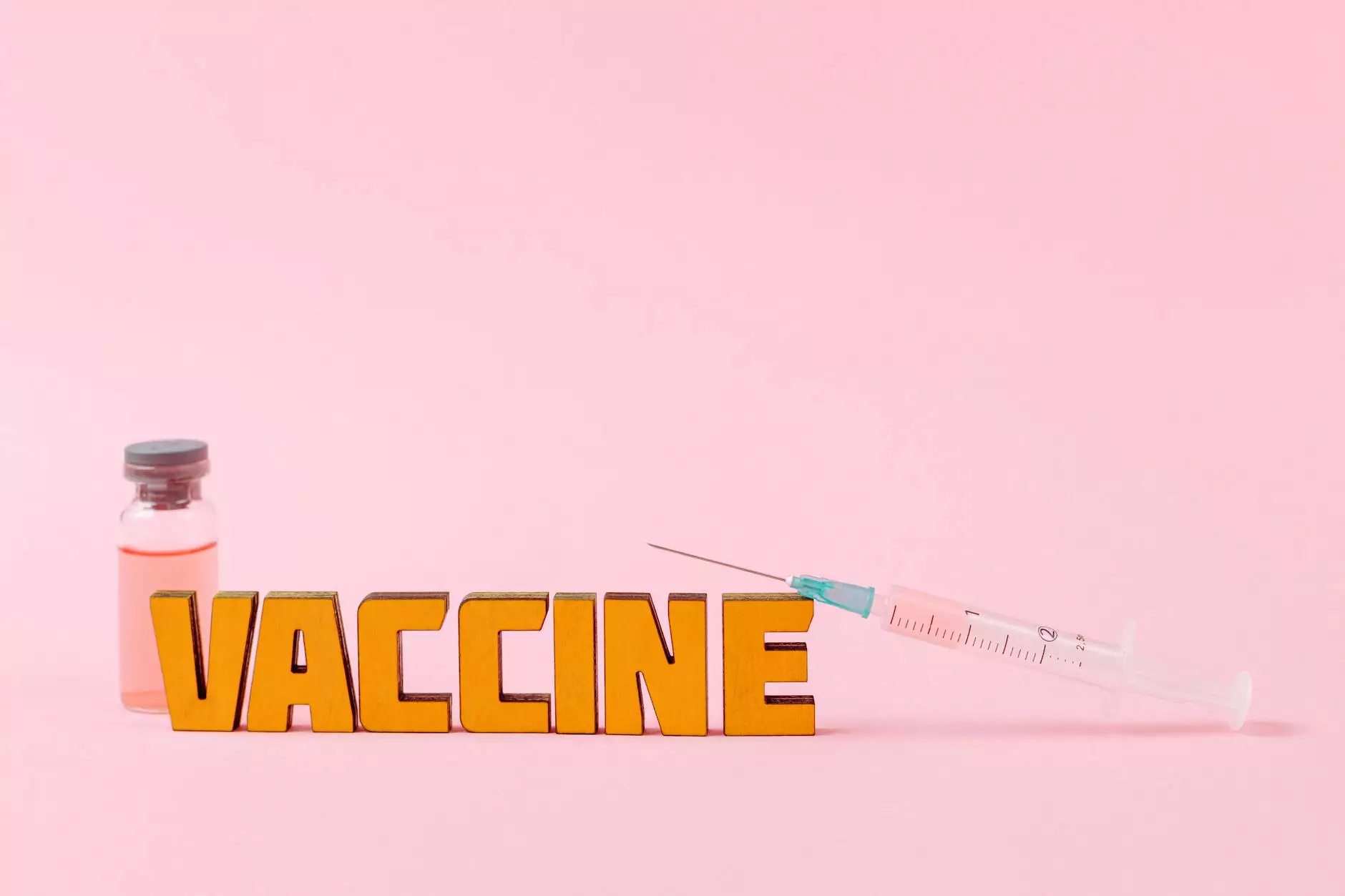
In the ever-evolving field of manufacturing, precision injection molding has emerged as a vital processing technique that serves industries ranging from automotive to consumer goods. This article delves deep into the intricacies of precision injection molding, its benefits, processes, and significance in the realm of metal fabrication. We’ll explore how businesses such as deepmould.net are leveraging this technology to gain a competitive edge.
What is Precision Injection Molding?
Precision injection molding is a manufacturing process characterized by its ability to create complex, detailed parts with high accuracy and repeatability. The method involves injecting molten material into a precisely-designed mold, where it cools and solidifies into the final product. This process is particularly beneficial for producing large volumes of identical items, making it an indispensable technique in various industries.
Key Benefits of Precision Injection Molding
Understanding the core advantages of precision injection molding allows businesses to evaluate its potential impact on their production processes. Here are some of the most significant benefits:
- High Efficiency: The ability to produce a large number of parts quickly reduces labor and overhead costs, enabling manufacturers to meet demand efficiently.
- Complex Geometries: Precision injection molding can create intricate components that would be difficult or impossible to manufacture with other methods.
- Consistency: The process guarantees uniformity across parts, ensuring that each product meets specified tolerances.
- Material Versatility: A variety of thermoplastics and thermosetting polymers can be used, allowing for flexibility in design and application.
- Customizability: Various modifications can be made to molds and materials for specific product requirements.
The Precision Injection Molding Process
The workflow of precision injection molding involves several critical steps that ensure the successful creation of high-quality products. Here’s a detailed overview of the process:
1. Design and Engineering
The initial stage includes designing the part and mold using specialized CAD (Computer-Aided Design) software. Engineers focus on every detail, from dimensions to wall thickness, ensuring the design meets functionality and manufacturability criteria.
2. Mold Fabrication
Once the design is finalized, the mold is fabricated, typically from steel or aluminum. This step requires precision machining and might include processes such as EDM (Electrical Discharge Machining) for intricate designs.
3. Material Selection
The next step involves selecting the appropriate material. Options may include various plastics, metals, or composites, depending on the end-use of the component.
4. Injection
In this stage, the chosen material is heated until it becomes molten and is injected under high pressure into the mold cavity. The precision of this step is vital, as it must fill all areas of the mold evenly.
5. Cooling and Ejection
After injection, the material cools and solidifies. Once this stage is complete, the mold opens, and the finished part is ejected. The cooling time can significantly affect the cycle time, making it a critical factor in process efficiency.
Applications of Precision Injection Molding in Metal Fabrication
While primarily associated with plastics, precision injection molding has valuable applications in metal fabrication as well, particularly in creating metal parts and components through innovative methods such as:
- Metal Injection Molding (MIM): A process where fine metal powders are mixed with binders and injected into molds, allowing for high precision and complex geometries.
- Thermal Injection Molding: Combining heating elements in the injection molding process for better metal flow and filling.
- Hybrid Molding Techniques: Utilizing a combination of materials in one mold to create composite parts with enhanced properties.
Challenges and Considerations in Precision Injection Molding
Despite its many advantages, businesses must navigate several challenges when implementing precision injection molding. Key considerations include:
1. High Initial Costs
The upfront expenses associated with creating molds can be substantial, making it essential for businesses to align their budget with production volumes.
2. Material Limitations
Not all materials are suitable for injection molding, and understanding material properties is critical to ensuring product quality.
3. Design Complexity
Designing components for precision injection molding requires expertise to avoid potential failures such as warping or inadequate filling.
The Future of Precision Injection Molding
As industries increasingly demand efficiency and customization, the future of precision injection molding appears promising. Here are some trends shaping its evolution:
- Automation: The integration of robotics and automation technologies is streamlining processes further, enhancing reliability and speed.
- Sustainable Practices: Increasing focus on eco-friendly materials and energy-efficient machines is transforming the landscape of manufacturing.
- Advanced Software Solutions: Innovations in simulation software are allowing for better mold design and process optimization, reducing lead times and costs.
Choosing the Right Partner for Precision Injection Molding
Partnering with an expert in precision injection molding is crucial for businesses aiming to leverage this technology effectively. Here are key factors to consider:
1. Experience and Expertise
Evaluate potential partners based on their industry experience and technical knowledge, particularly in dealing with your specific product requirements.
2. Quality Assurance
Look for companies that adhere to stringent quality control processes and have certifications that bolster their reliability.
3. Technical Capabilities
Consider the partner's capabilities in material selection, mold making, and production scaling to ensure they can accommodate your needs from start to finish.
Conclusion
In conclusion, precision injection molding represents a cornerstone of modern manufacturing with unparalleled advantages in efficiency, precision, and versatility. As industries continue to evolve, staying ahead of the curve with innovative techniques will be paramount to maintaining a competitive edge. Businesses like deepmould.net epitomize the blend of cutting-edge technology and expert knowledge that drives manufacturing forward. Investing in precision injection molding is not just about producing parts; it’s about embracing the future of manufacturing, where precision meets functionality and innovation fuels growth.