Understanding High Pressure Die Casting Suppliers
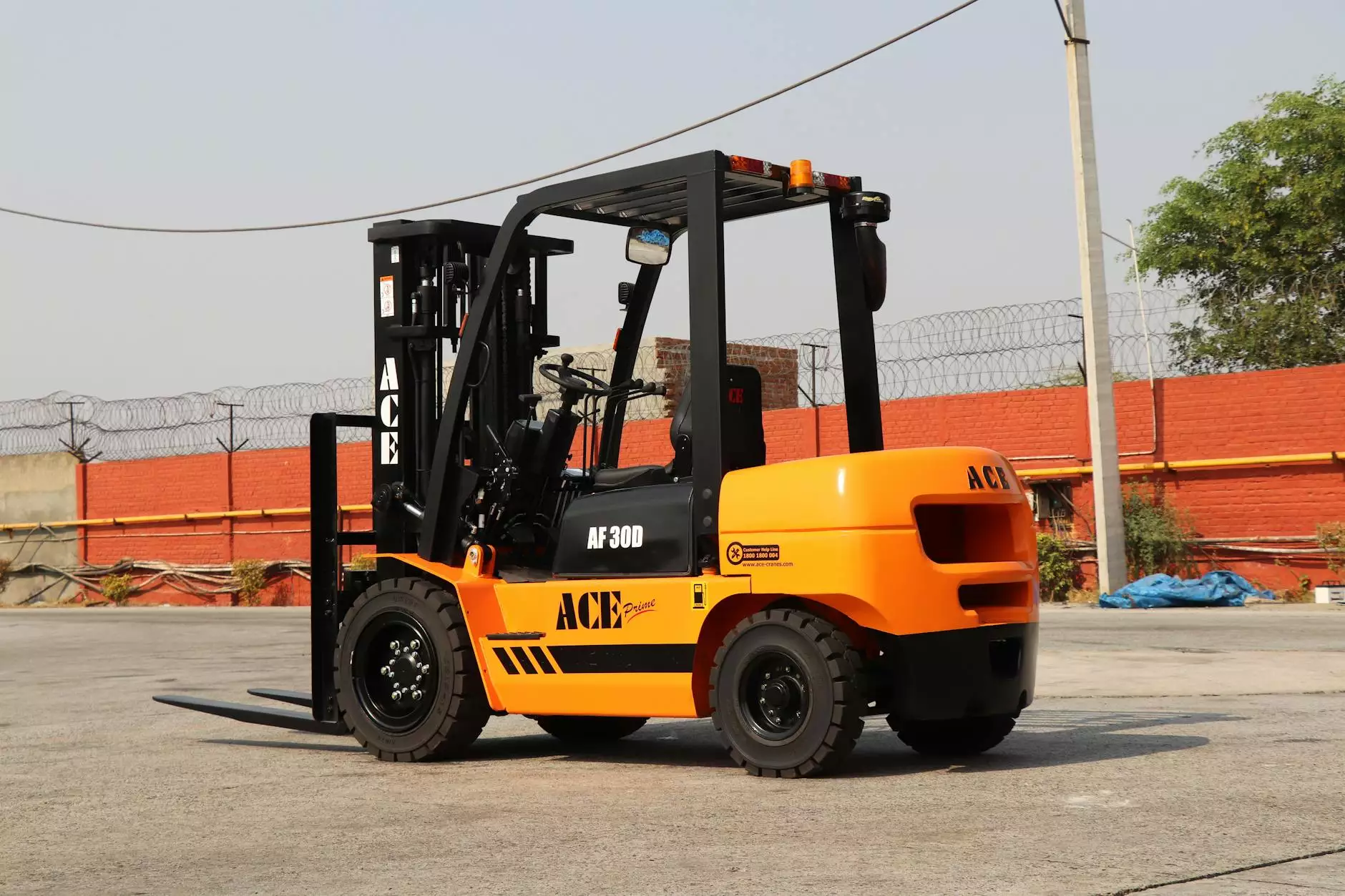
In the modern manufacturing landscape, the demand for precision-engineered components has surged dramatically. This trend has significantly propelled the high pressure die casting suppliers to the forefront of metal fabrication. High pressure die casting (HPDC) is a highly efficient process used to produce intricate metal components from non-ferrous alloys such as aluminum, magnesium, and zinc. This article aims to provide a comprehensive overview of high pressure die casting, the advantages it offers, applications, and critical factors to consider when selecting a supplier.
What is High Pressure Die Casting?
High pressure die casting involves forcing molten metal into a mold cavity at high pressure. This method allows for the production of complex geometries with high dimensional accuracy and excellent surface finish. The process consists of several key steps:
- Melting: The metal is heated in a furnace until it reaches a molten state.
- Injection: The molten metal is injected into a steel mold under high pressure.
- Cooling: The metal cools and solidifies within the mold.
- Extraction: The solid component is ejected from the mold for further processing.
Advantages of Using High Pressure Die Casting
The popularity of HPDC stems from its numerous benefits, which include:
- High Precision and Accuracy: The process yields components with tight tolerances and intricate details.
- Excellent Surface Finish: HPDC offers superior surface quality compared to other casting methods, reducing the need for additional machining.
- Efficiency: High production speeds and the ability to recycle scrap metal contribute to reduced manufacturing costs.
- Material Versatility: It accommodates a range of alloys, providing great flexibility for manufacturers.
Applications of High Pressure Die Casting
High pressure die casting is utilized across various industries, showcasing its versatility and efficiency. Key applications include:
- Automotive Industry: Components such as engine blocks, transmission cases, and structural parts.
- Aerospace Sector: Lightweight, high-strength parts essential for aircraft performance.
- Consumer Electronics: Housings for devices like smartphones and laptops that require precise dimensions.
- Medical Devices: Components requiring stringent tolerances and high-quality finishes for healthcare applications.
How to Choose the Right High Pressure Die Casting Supplier
Choosing the right supplier is crucial for ensuring the success of your manufacturing processes. Here are several factors to consider:
1. Industry Experience
Evaluate the supplier's experience in high pressure die casting. A supplier with a proven track record will have a deep understanding of best practices, material properties, and process optimizations.
2. Quality Assurance
Look for suppliers who follow stringent quality control protocols. Certifications such as ISO 9001 indicate a commitment to maintaining high-quality standards.
3. Material Capabilities
Ensure the supplier has access to a range of materials suitable for your specific applications. The ability to work with different alloys can enhance your product design options.
4. Technological Advancements
Suppliers that invest in modern technology and automation can often deliver superior products and shorter lead times. Look for those utilizing advanced die casting machines and simulation software.
5. Customer Support
Reliable customer support is essential for addressing issues that may arise during production. A supplier that offers responsive communication can significantly ease the manufacturing process.
Deep Mould: A Leading High Pressure Die Casting Supplier
Among the prominent high pressure die casting suppliers, Deep Mould stands out for its specialized services in the metal fabrication category. With years of experience and a commitment to quality, Deep Mould offers comprehensive solutions tailored to meet the unique needs of various industries.
Why Choose Deep Mould?
- Expertise: Deep Mould’s team comprises seasoned professionals who leverage their extensive knowledge to deliver high-quality products.
- Advanced Facilities: The state-of-the-art manufacturing facilities utilize the latest technology to ensure precision and efficiency.
- Customization: They offer tailored solutions to meet specific project requirements, including design adaptability and material selection.
- Commitment to Quality: Deep Mould adheres to rigorous quality standards, ensuring that all products meet or exceed client expectations.
Conclusion
In summary, high pressure die casting suppliers play a vital role in meeting the manufacturing demands of today’s industry. The advantages of high pressure die casting, coupled with the right supplier, can dramatically enhance production quality and efficiency. When selecting a supplier, consider their experience, quality assurances, material capabilities, use of technology, and customer support.
Embrace the innovation and efficiency of high pressure die casting by partnering with proven suppliers like Deep Mould, and watch your manufacturing capabilities go to new heights.